How Can You Prevent Sediment and Blockages in Oil Pressing?
Oil pressing sediment and blockages halt your production. They reduce your output. They also waste your time and money. We understand these frustrations in edible oil production. This article gives you clear steps. You will learn how to avoid common problems. We explain how to keep your whole industrial oil mill plant running smoothly. You can achieve better oil quality and higher yields.
Last updated: February 2025 | Estimated reading time: 15 minutes
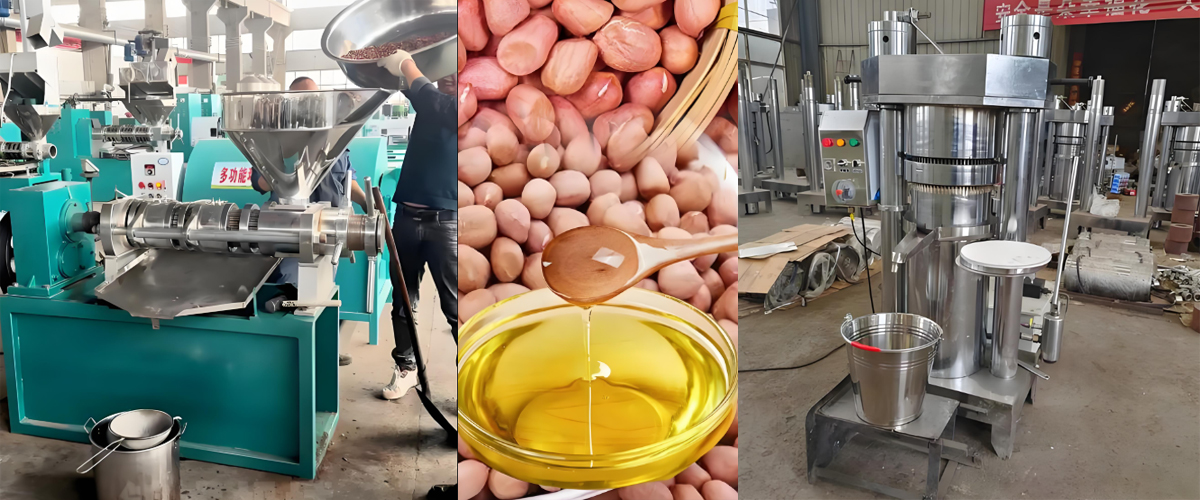
This article will help you:
- Understand common causes of oil press issues?
- Learn how to remove sediment effectively?
- Improve your oil processing efficiency?
- Discover new oil technology?
Why Do Oil Press Sediment and Blockages Happen?
Oil press sediment and blockages happen for clear reasons. Poor raw material preparation is a main cause. This includes materials with too much moisture or impurities. These unwanted particles can stick inside the machine. This leads to blockages. This makes your equipment work harder, or stop completely. You need to prepare your materials well.
When materials are not clean, small pieces of husks, dirt, or other foreign matter can mix in. These tiny pieces slowly build up inside the press chamber. Over time, they form hard plugs. These plugs restrict the flow of oil and cake. This reduces your output. It also puts stress on the machinery. You need to remove these impurities. You can lose money if you do not do this. Avoiding these issues saves you repair costs and time. Your equipment will last longer.
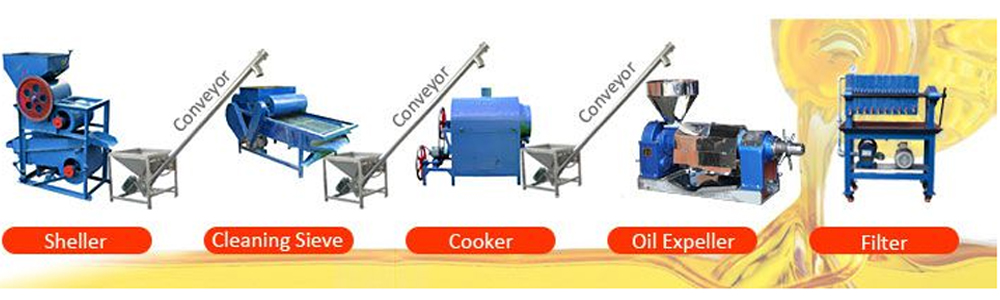
Understanding Raw Material Pre-treatment Impact?
Raw material pre-treatment equipment is very important. Without proper cleaning, drying, or cooking, issues appear. For example, wet seeds can become gooey inside the press. This sticky material clogs the screw or the filter plates. Too much moisture also reduces oil yield. Dirty seeds bring sand and stones. These can wear down your oil extraction equipment. This causes damage. Proper pre-treatment avoids these problems.
Imagine you are making juice. If you put whole fruit with stems and seeds directly into a juicer, it gets stuck or breaks. Oil pressing is similar. When we process raw materials like peanuts, sunflower seeds, or soybeans, they must be clean. They must have the right moisture level. If large pieces of shell or uncrushed nuts go into the press, they stop the flow. If seeds are too moist, they create a paste. This paste blocks the flow paths. Pre-treatment steps include cleaning, shelling, crushing, cooking, and adjusting moisture. Each step helps the material flow better. This reduces wear and tear on your equipment. This lets your single screw oil press or double screw oil press work at its best. This also ensures you get pure oil.
Pre-treatment Step | Problem It Prevents | Your Benefit |
---|---|---|
Cleaning/Screening | Sand, stones, foreign matter | Reduces equipment wear, prevents blockages |
Dehulling/Shelling | Hard shells, husks | Increases oil yield, reduces sediment |
Crushing/Flaking | Large, irregular pieces | Ensures even pressing, prevents clogging |
Cooking/Steaming | Raw material stickiness | Improves oil flow, enhances yield |
Drying/Moisture Control | Excess moisture, material becoming paste | Reduces clogging, ensures better oil separation |
Practical Tips for User:
- Clean your raw materials thoroughly: Use screening machines to remove large impurities.
- Control moisture levels carefully: Use drying equipment like a roasting machine or a dryer to reach the ideal moisture content for your specific material.
- Process materials uniformly: Use crushers or flakers to get consistent particle sizes.
Actual Case Study: A small oil mill in Africa struggled with frequent blockages. They processed sunflower seeds. We found they skipped the drying step. The seeds had high moisture. This created sticky residue. After implementing a pre-drying process, their blockages dropped by 70%. Their oil yield went up by 15%. This shows the power of good pre-treatment.
How Does Equipment Design Affect Blockages?
The internal design of your oil pressing equipment plays a big role. Some designs are more prone to blockages. For example, older screw designs might have less efficient cake discharge. This causes accumulation. Small clearances or rough internal surfaces can also trap sediment. Our modern equipment is designed to minimize these issues. We ensure smooth flow paths.
Poorly designed screw oil press machines often have tight spaces or sharp corners inside the pressing cage. These areas become accumulation points for sediment. The oil cake, which is the solid residue after oil extraction, needs to move smoothly out of the machine. If the cake discharge port is too small or if the screw design does not push the cake out efficiently, it builds up. This causes back pressure. This leads to blockages. Our engineers consider every detail. They create designs that allow for easy flow. They minimize dead zones where sediment can settle. This ensures continuous operation. It also makes cleaning easier.
How Do You Effectively Clean Oil Pressing Equipment?
Effective cleaning is key to preventing oil press sediment and blockages. Regular cleaning removes build-up. This keeps your machine running well. You need a consistent cleaning schedule. This stops small issues from becoming big problems. Cleaning also maintains oil quality.
Cleaning is not just about clearing current blockages. It is about preventing future ones. After an oil pressing cycle, some oil residue and cake particles always remain inside the machine. If these are not removed, they harden over time. They become difficult to break down. This build-up restricts oil flow. It also reduces the machine’s efficiency. You need to use the right tools. You need the right methods for cleaning. This includes disassembling parts when necessary. This also means using appropriate solvents or hot water. A clean machine delivers consistent performance. It also extends its lifespan.
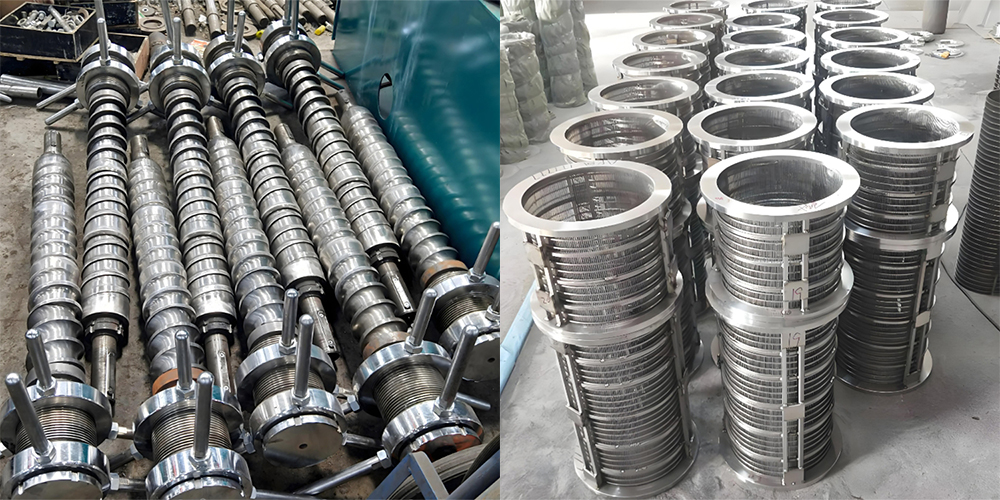
What Tools and Methods Help With Sediment Removal?
You need specific tools for sediment removal. Brushes, scrapers, and high-pressure air or water guns are useful. For tough build-ups, you might need specialized chemical cleaners. You must follow safety guidelines when using chemicals. Disassembling key parts, like the pressing cage or screw, allows for thorough cleaning. This clears deep blockages.
When you disassemble your oil extraction equipment, you can reach all parts. This includes the pressing worm, pressing ring, and oil outlet slots. Hot water or steam can soften hardened oil residue. You can then use brushes or scrapers to remove it. For very stubborn deposits, specific food-grade solvents can help. Always make sure these solvents are safe for your equipment and do not leave harmful residues. After cleaning, dry all parts thoroughly before reassembly. This prevents rust. It also ensures smooth operation. A clean machine performs much better.
Cleaning Tool/Method | Purpose | Your Practical Use |
---|---|---|
High-pressure air/water | Loosens soft residue | Blow out loose particles from press cage |
Stiff brushes/Scrapers | Removes hardened cake | Scrape inside the press barrel and screw |
Hot water/Steam | Softens oil residue | Soak disassembled parts to loosen grime |
Food-grade solvents | Dissolves tough build-up | For deep cleaning of sticky areas, follow safety guide |
Disassembly | Access internal parts | Allow you to clean every nook and cranny |
Practical Tips for User:
- Establish a cleaning schedule: Clean minor parts daily and major components weekly or monthly, depending on usage.
- Train your staff: Ensure everyone knows the proper cleaning procedures and uses the correct tools.
- Use appropriate cleaning agents: Choose non-corrosive, food-grade cleaners for your equipment.
Actual Case Study: A client running a hydraulic oil press reported decreased efficiency. The oil flow was very slow. We advised them to fully disassemble and clean the press cylinder and filter plates. They found significant sediment build-up. After a deep clean, the press output increased by 25%. They also noticed higher oil quality. This showed the importance of thorough cleaning.
Can Regular Maintenance Prevent Clogging?
Yes, regular maintenance is vital. It stops clogging before it starts. This includes checking all parts. You should also replace worn components. Lubricating moving parts ensures smooth operation. A good maintenance plan reduces sediment accumulation. It prevents unexpected breakdowns. This is crucial for your oil mill plant longevity.
Regular maintenance is like giving your car an oil change. You do it to prevent bigger problems. For oil pressing equipment, this means inspecting the screw, pressing cage, and bearings. Look for signs of wear and tear. A worn screw, for example, will not push material efficiently. This can cause congestion. Regular lubrication prevents friction. It reduces heat build-up. This minimizes the chance of oil residue hardening inside the machine. You also need to keep records of your maintenance. This helps you track performance. It helps you identify recurring issues. Preventative maintenance saves you from costly repairs down the road. It ensures consistent output.
What Are the Best Practices for Oil Pressing Efficiency?
Achieving high oil pressing efficiency means more than just pressing oil. It involves optimizing every step. This starts from raw material handling. It goes through filtration and refining. Using the right techniques ensures maximum oil extraction. It also yields the highest quality oil. This also minimises waste and costs.
Efficient oil pressing is a holistic process. It is not just about the pressing machine itself. It includes how you receive and store your raw materials. It involves the temperature and pressure settings during pressing. It also covers what you do with the oil after it leaves the press. Every stage can impact the final oil quality and yield. You need to consider the whole production line. This helps you find areas to improve.
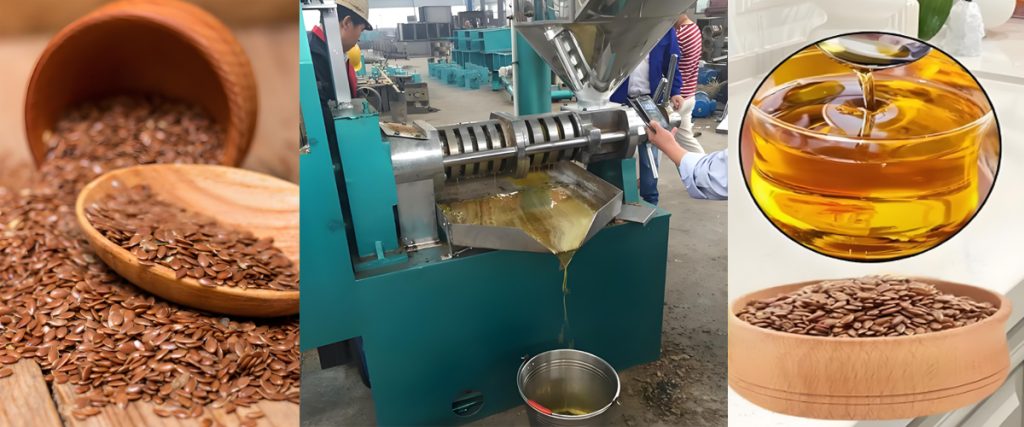
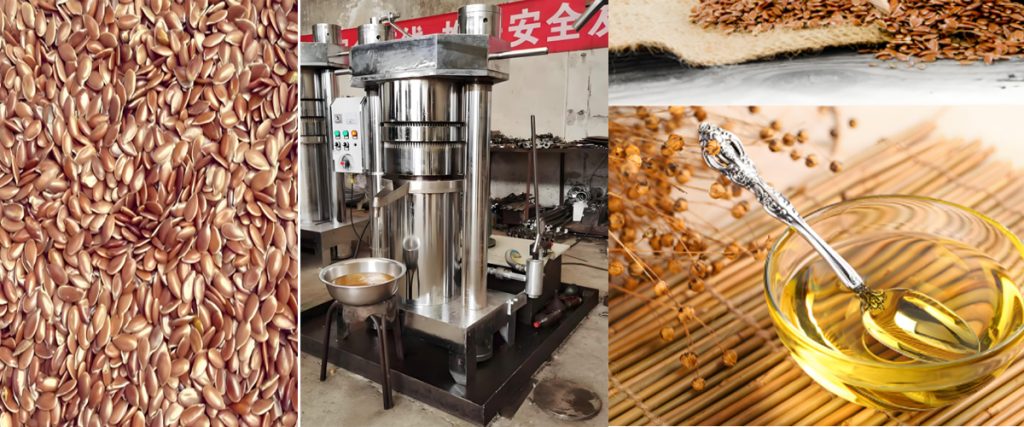
How Can Filter Equipment Improve Oil Quality?
After pressing, oil contains fine particles. These are suspended solids. These come from the raw material. This makes the oil cloudy. It reduces its shelf life. Filtering equipment removes these impurities. This improves the oil’s clarity. It also enhances stability. This step is essential for producing high-quality edible oil. A centrifugal oil filter can quickly separate solids. A vacuum oil filter can remove fine particles and moisture.
Filtering is a critical step in producing good oil. Imagine trying to drink a beverage with sandy particles inside. You would not like it. Oil is similar. Even after pressing, small bits of seed residue, protein, or moisture remain. These make the oil look cloudy. They can also cause it to spoil faster. Filter machines work by passing the oil through fine screens or filter cloths. These catch the solid particles. Centrifugal filters use high-speed spinning to separate solids from liquids. Vacuum filters draw oil through a porous medium using suction. This process makes the oil clear. It also extends its shelf life. Clean oil sells better. It also meets higher standards for edible use. This is a must for any professional oil producer.
Why is Oil Refining Equipment Critical for Purity?
For truly pure, high-grade edible oil, oil refining equipment is necessary. Pressing oil is the first stage. Refining is the second, most advanced stage. This equipment removes unwanted substances. These can affect taste, smell, color, and stability. Refining makes oil safe for consumption. It also meets international standards. Our refinery equipment can perform degumming, deacidification, decolorization, and deodorization.
Refining oil is like polishing a diamond. It takes a good product and makes it excellent. Crude oil from the press still contains various impurities. These include phospholipids (gums), free fatty acids, pigments, and odor-causing compounds.
- Degumming removes phospholipids. These can cause cloudiness. They also make the oil sticky.
- Deacidification removes free fatty acids. These make the oil taste sour. They reduce its shelf life.
- Decolorization removes pigments. This makes the oil look clear and bright.
- Deodorization removes bad odors. This gives the oil a neutral, clean smell.
These processes ensure the final product is stable. It also has a long shelf life. It meets strict food safety requirements. Whether you are using a batch refining equipment or a continuous system, modern refining offers peak purity. For large edible oil processing factories, this level of purity is not just a preference. It is a requirement for market success.
2025 Latest Developments in Oil Processing Technology?
In 2025, oil processing technology continues to evolve. New machines are more efficient. They are also more automated. We see advances in smart sensors. These can detect sediment buildup early. They can also optimize pressing parameters in real time. Oil extraction equipment is becoming smarter. It requires less manual intervention. This increases productivity.
Latest progress in our field focuses on making machines more self-sufficient and precise. Imagine equipment that almost thinks for itself. New intelligent control systems use advanced algorithms. They monitor the pressing process with high accuracy. These systems can adjust temperature. They can change pressure. They can also alter feed rate. This happens automatically. This prevents oil press sediment accumulation. It maximizes oil yield. These systems also reduce energy use. They integrate seamlessly with other units on the oil processing line. This leads to a truly continuous and highly efficient operation. This means less downtime for you. It means more consistent output.
Latest Progress Overview:
- AI-driven optimization: Systems now use artificial intelligence to predict and prevent blockages based on real-time data.
- Modular designs: Equipment is more modular, allowing easier expansion and maintenance, and faster part replacement.
- Advanced filtration materials: New filter materials offer higher efficiency and longer lifespan, reducing cleaning frequency.
Market Insight: The demand for automation in oil extraction equipment is growing fast. Especially in developing countries. They seek cost-effective and reliable solutions. These solutions minimize labor and maximize output. Our factory direct sales model helps meet this need. We provide competitive prices. Our global exports show our widespread impact. We serve over 120 countries now. This reflects our strong position in the market.
What Questions Do People Ask About Oil Press Maintenance?
Question 1: How often should I clean my screw oil press?
You should clean your screw oil press daily after each use. A deep clean, disassembling key parts, is needed weekly or monthly. This depends on your usage. This stops sediment buildup.
Question 2: Can I use any oil to lubricate my oil press machine?
No, you must use specific food-grade lubricants for your oil extraction equipment. This prevents contamination of the edible oil. Check your machine’s manual for the correct type.
Question 3: What is the best way to unclog a deeply blocked oil press?
For deep blockages, first, turn off and cool down the machine. Then, carefully disassemble the pressing chamber. Use sturdy scrapers and brushes. Hot water or steam can help loosen hardened sediment. Always follow safety protocols.
Question 4: Does choosing the right raw material matter for preventing clogs?
Yes, absolutely. Using clean, properly prepared raw materials with ideal moisture content significantly reduces blockages. This protects your machine. It also increases your oil yield. Always start with quality material.
Question 5: What is the lifespan of an oil press screw, and when should I replace it?
The lifespan of a screw depends on use and material. It is usually 1-3 years. Look for wear signs. These include a reduced oil yield. Also look for increased cake residue. Replacing worn parts on time prevents serious blockages. It also maintains efficiency.
Summary and Recommendations
Preventing oil press sediment and blockages is crucial. It ensures your oil production is smooth and profitable. You must focus on three key areas. First, meticulous raw material pre-treatment. Second, regular and thorough cleaning. Third, consistent equipment maintenance. These steps are simple but powerful. They will boost your oil quality and yield.
We encourage you to revisit your current processes. Look for areas to improve. Invest in proper pre-treatment equipment. This includes efficient cleaning and drying machines. Implement a strict cleaning schedule. Train your staff well. Consider upgrading to more automated and smart machines for better efficiency. Our experts are ready to help you optimize your entire oil mill plant.
About Fude Machinery
We are Fude Machinery, a leading Chinese oil processing equipment manufacturer. Our base is in Zhengzhou, China. We specialize in B2B solutions. We offer a full range of equipment. This includes oil extraction equipment, refining machines, and complete processing lines. Our products serve edible oil, refined oil, and fat processing industries. We provide comprehensive solutions. We work with clients from small farms to large oil groups. Our products reach over 120 countries. We focus on quality and customization.
Contact Us
Ready to improve your oil processing efficiency? Do you want to reduce blockages and increase yield? Visit our website or call us today. Our team can give you a free consultation. We offer customized solutions for your unique needs. Contact us now for a consultation!
Related recommendations
-
Difference between hydraulic press and screw press
174How Do Their Working Principles Fundamentally Differ?Hydraulic Press: The Slow StrongmanScrew Press: The Continuous WorkerWhat Raw Materials Does Each Press Handle Best?Hydraulic Press Specialties:Screw Press Mainstays:How Do They Compare on Oil Y...
View details -
Understanding oilseeds before starting an oil press?
152Why Must You Understand Oilseeds Before Investing in Oil Pressing Equipment?Soybeans (Soybean): One of the World's Most Important Oilseeds, What Are Its Oil and Processing Characteristics?Rapeseed/Canola (Rapeseed/Canola): High Yield and Adaptable...
View details -
Small oil press equipment
128Mini Oil Mill Machinery AdvantagesComprehensive functionality, addressing different user needs The mini oil mill is a series of machines used to extract oil from various oil bearing seeds. They include: ground nuts, sesame, sunflower, cotton see...
View details -
What are the applications of refining machines in the petroleum industry
298Refiners (refined oil equipment) are widely used and important in the petroleum industry. They convert crude oil into various high-quality petroleum products through a series of complex processing procedures
View details
HelloPlease log in